fan powder coating paint lines systems , this powder coating line is specially designed to provide quality powder coating fan
It consists of automatic powder coating booth with reciprocator and automatic powder coating gun,powder recycling unit,powder supplying hopper, electrical/diesel/LPG fired camel bake oven,monorial conveyor unit and control panel.
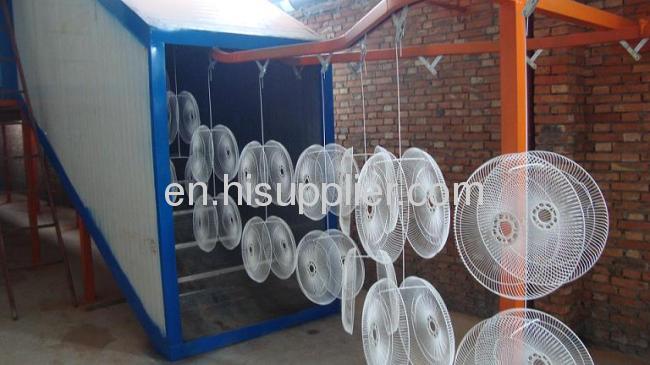
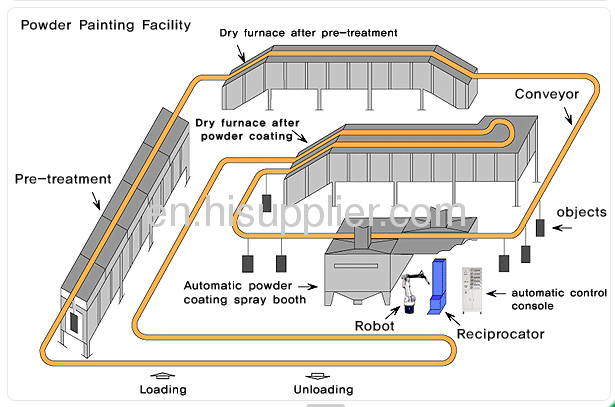
Wehave specialized engineers to design and manufacture automatic plantswith various processes as per customers requirement.This plant consistsof several processes which are made into one by our specialized design.
asingle continuous powder coating process, whereby items are attached toan automated track, which subsequently travels through four separatepowder coating process stages.This process delivers a pre-treated andfinished powder coated component at the end of the track.
Process One - Pre-treatment
Pre-treatment is a five stage process comprising of the following:
Stage 1: Is a highly Alkaline cleaner for steel alloys and zinc-coated steels
Stage 2: Cold rinsing from the main water supply.
Stage 3: Rinsing with De-mineralised water
Stage 4: silane-based multi-purpose liquid pre-paint treatment
Stage 5: Single ring rinsing with De-mineralised water
Process Two – Drying
A drying oven set at approximately 180°C complements the pre-painttreatment and rinse water process, to give an ideal substrate for powderapplication.
Process Three – Powder application
A combination of automatic and manual spray operations ensures that a controlled and consistent powder film build is achieved.
Aswork passes through the spray booth, controlled amounts of powder areapplied by automatic Electro-static spray guns mounted on reciprocators.Difficult areas not reached by this process are coated by anindependent manual spray operation.
double door spray booth
ITEM | NAME | QTY | SIZE(L×W×H) | REMARK |
1), | Double door spray booth | 1set | 7000×1500×2900 | |
| Operation size | 2pcs | 900×1600mm(W×H) | |
| Open size | 2pcs | 700×1800mm(W×H) | |
| Body material | | δ=1.2mm cold plate, fold production | |
| Air velocity | | 0.5-0.7m/s | |
| light | 2pc | 2-40W/set | |
2) | Recovery | 1pc/set | | |
| Type | | Single Cyclone and Pulse blowback filters | |
| Process Wind flow | Single set | 18000m³/h | |
| Fliter number | 9pcs/set | Flither sizeφ325×1200mm | fast-loading |
| Pulse Solenoid valve | 9pcs/set | | |
| Filter rotor body | 9pcs | | |
| Recycling fan | 1pcs/set | | Motor power:18.5KW |
3) | Manual Powder coating machine | 2pcs | COLO-500PGC1 | |
| Automatic Powder coating machine | 2pcs | COLO-500PGC1 -A | |
| 2m travel receprotator | 2pcs | COLO-2100D | |
Process Four – Curing
After
powder coating, the work pieces pass through a gas fired tunnel oven.
Thedeposited powder film flows then cures as the metal temperatureincreases to that recommended for the powder applied. During the courseof this process, the particles of powder bond together to produce acontinuous smooth finish.
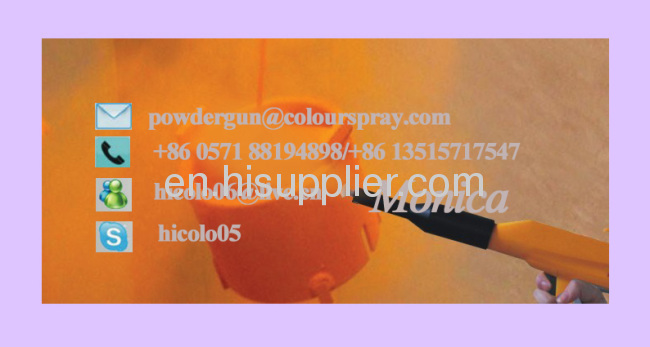