The applicable fuel of ZG Series Inner Circulating Fluidized Bed Boiler is lean coal,bituminous coal,anthracite coal,lignite,chain slag admixture.
This type of ZG Series Inner Circulating Fluidized Bed Boiler has the following characteristics:
1.The use of membrane water cooling wall to layout the combustion chamber,separator and fly back feeding system into one,has compact structure,the separator has unique structural design.A.separator use of membrane wall to form the framework,structure is stable.B.the membrane wall can absorb heat of the lining,allowing residual carbon in the flue gas to continue burning in the separator,will not cause coking and enhance the separation efficiency.C.membrane wall are welded inverted fork type grasping nails,wear-resistant material forming cast to ensure a smooth inner surface of the separator,and is a special streamlined,separation efficiency is as high as 97.97%,cutting diameter dc is for 8-15um.D.lined with abrasion-resistant material with thickness of 80mm,of small thermal inertia,at the same time can prevent cracks,and meet the requirement of ZG Series Inner Circulating Fluidized Bed Boiler to start and stop quickly.
2.The back feeding system uses patented technology diaphragm wall porous semi-gravity loopback device,the back feeding materials is expected to flow evently.A.the back feed road is formed by two membrane water cooling wall,part of the heat carried by fly ash will be absorbed by the diaphragm wall pipe and reduce temperature of fly ash,the back feed road will not have coke caused by the post-combustion.B.the loopback device using patented technology of porous semi-gravity wall type loopback device.when the ash flies back into the combustion chamber, the ash will layout evenly along the direction of furnance arrangements, uniform feed back.C.the use of loose wind can adjust the amount of feeding back material.
3.The wear-resisting design has applied a number of measyres.A.the use of low-speed ZG Series Inner Circulating Fluidized Bed Boiler design,combustion chamber has large cross-sectional area,and smoke speed is low,low flue gas dust concentration.B.the separator is designed in the exit of the combustion chamber,applies high-temperature separation method to prevent effectively the wearing of heating surface behind the separator.C.the oulet of separator was designed the furnance the secondary purification separated device.D.at the upper part of combustion chamber where the fly ash has high concentrations,smoke speed is high,water-cooled film wall was painted high temperature resistant and wear-resistant materials,to avoid film wall to be worn.
4.The design of pipe wear-resistant.A.pipe using welding wear bars with the special angle and size to prevent wear on the tubular pipe.B.After a period of time(usually more than one year)can take measures such as welding wear bars,pipe life can be extended indefinitely.
5.Combustion devices use of hood,porous form,so that the wind is uniform,the quality of flow is uniform and stable.
6.Fuel adaptability.Combustible not only with anthracite,lean coal,bituminous coal,in particular,can burn with coal gangue,chainslag,blast furnance gas and low-grade fuel that other burning furnance can not burn.
7.ZG Series Inner Circulating Fluidized Bed Boiler can be continuonsly operated for a long time,very low failure rate.The longest running time is up to 10 consecutive months,the running time about 350 days in one year.
Inner Circulating Fluidized Bed Boilers
1.Output:rated evaporation:20-75 t/h
2.Structure:water tube
3.Style:vertical
·Products List
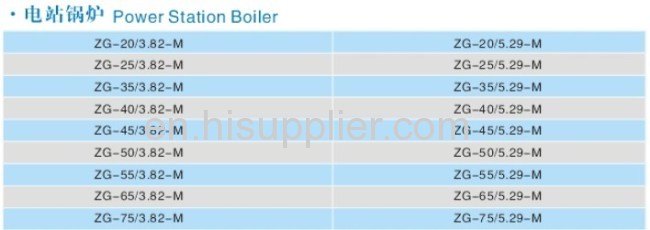