LED Assembly lead free Reflow Oven A600
SMT Lead Free Small Reflow Oven (A600) for PCB LED AssemblyModel: A600 MID-sized Lead-free Reflow Oven(6-zone)
Brief: Lead-free reflow soldering
Heating System
> Eight groups of top and bottom forced hot air convection heating zones.
> Patented heating plates in each zone uniformly transfer heat to the PCBs using forced hot air convection.
> Independent temperature control in each zone to ensure temperature uniformity within the process tunnel.
> Power consumption savings of 1/3 as compared to other systems.
> Patented motorized blower in each zone is designed to ensure stable air pressure, withstand high process temperature and is disturbance-free.
> Audible and light tower alarm for temperature limits and blower malfunction.
> Fast start-up (within 20 minutes) from room temperature to work temperature due to the high efficiency of the motorized heating plates.
Cooling System
> Two (2) groups of air fans convection cooling zones.
> Mesh belt conveyor system
> Closed-loop computer control of the conveyor provides a precise and repeatable reflow process.
Control System
> PC control system with windows based control software.
>Lenove Computer and Siemens PLC
Additional Features
> Integrated UPS will be automatically activated in case of main power failure and will keep control PC and conveyor running for minimum 5 minutes to send out PCBs inside the oven tunnel.
> Three (3) profiling ports and integrated profiling software are designed for convenient temperature profiling.
> Swing arm control PC station
> Two (2) emergency stop switches
> Two (2) exhaust port
Specifications | A-600(Mid-sized 6-Zone) |
General |
Outside Dimension(L*W*H) | 3600x720x1250mm |
Standard Color | Computer Grey |
Weight | Approx. 420KG |
Number Of Heating Zones | Up6/Bottom6 |
Length Of Heating Zones | 2300mm |
Exhaust Volume | 10M3/minx2 Exhausts |
Standard Feature Of Control System |
Electric Supply Required | 3phase, 380V 50/60Hz |
Power For Warm Up | 11KW |
Power Consumption | 4KW |
Warming Time | Approx. 20 minute |
Temp. Setting Range | Room Temp. --- 300 degree |
Temperature Control Method | PID Close Loop Control + SSR Driving |
Temperature Control Precision | ± 1.0 degree |
Temperature Deviation on PCB | ± 1.5 degree (by MR Board Test Standard) |
Heating Element | Especial Heating elements For Long Life ; |
Commutated Element | Aluminium Alloy Plate |
Max. Temp. Gap Between Preheat & Reflow Setting | 80 degree |
Max. Temp. Gap Between Preheat Zones Setting | 40 degree |
Max. Temp. Gap Between Reflow Zones Setting | 50 degree |
Abnormal Alarm | Abnormal Temperature (Extra-high / Extra-low Temp. ) |
Board Dropped Alarm | Tower Light: Yellow- Warming; Green-Normal; Red-Abnormal |
Features Of Conveyor System |
Rail Number | 0 Lane (With Rail is Option) |
Max. Width Of PCB | 290mm (Option: 410mm ) |
Components Clearance | Top/ Bottom Clearance of PCB is 20mm |
Converyor Direction | L→ R (Option: R→ L) |
Fixed Rail Side(With Rail) | Front Rail Fixed(Option: Rear Rail Fixed) |
Transmission Agent(With Rail) | Air-Reflow = Chain + Mesh , N2-Reflow=Chain(Mesh is option) |
Converyor Height | 900+/-20mm |
Converyor Speed Range | 300~2000mm/min |
Temp. Thermocouple Slot | Standard |
On Line Editing | Standard |
Cooling Method | Forced-Air (Standard) |
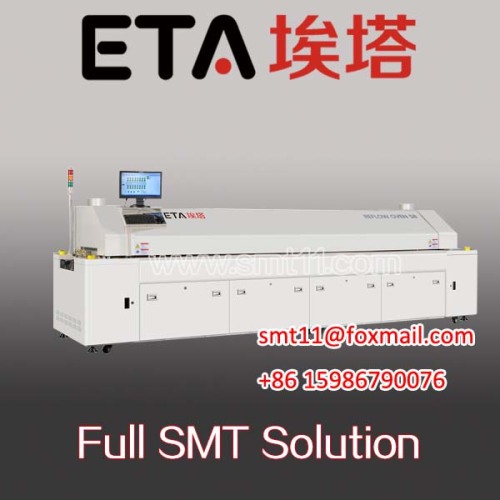