CNC Hydraulic Press Brake- Bending machine
Structural feature of machine
Outline structure should have these feature:
u Totally European design,streamlined looking
u Taking off inner-stress of welded parts by tempering,good stability
u Remove rust with sand-blast and coated with anti-rust paint
u Adopt Spanish pentahedron machine center,once clamping can finish all working surfaces which will guarantee dimension precision and position precision
u Supplying three front sheet supports
u Finish of Nippon Polyurethane paint
Ram structure
u Upper stroke design for bending,low noise,stable operating situation
u Parallel tolerance of Y1 and Y2 is 0.01mm
u Y1,Y2 can be programmed separately,can work under non-balance load,can bend cone-shape work piece
u At bottom dead center a pressure-keeping time is offered,and can be programmed to assure precision of all kinds of work piece.
u Can move the ram up slowly,which allows the operator to control work piece conveniently
u Universal fixing-surface of the upper tool can be meeting with the clamping requirement of the tool farthest
Hydraulic system
u Close loop electro-hydraulic synchronized servo-control system,the most advanced
u Hydraulic system is from Rexroth,Germany,a full loop electric-hydraulic proportional servo control,Sumitomo oil pump,Japan.
u Imported linear optical reader,guiding system,positioning system and hydraulic balancing system with high precision,which all can permit the processing work piece of full length or with eccentric.
u An outfit with "C" is at throat, as deformation compensation on throat,directly measuring the distance between upper tool and low die,assuring the precision of work piece.
u All seals in cylinder is imported,the most famous brand,good quality and high performance
u Overload overflow protection is outfitted to hydraulic system,which can assure no leakage,and the oil level can be read or seen directly
u Being able to work under rated load continuously,stable working and high precision
Back gauge
u Good for work piece needing multiple steps of bending with high precision requirement.
u X is moved with ball screw,guided by linear guide,and driven by digital AC servo-motor.
u Back gauge has well enough mechanical strength and rigidity with tank-type gauge structure.
u Two fingers are moving alone swallow guide,operate easily with high precision
u Particular finger-stop design,enlarge the range of back gauge.
Electrical system
u Electrical components are imported or from Sino-foreign joint Venture,in accordance with international standards,reliable safety,long life,good anti-interference ability,a radiation unit is fitted in electrical cabinet.
u Having a movable single-hand pedal switch with emergency stop,easy to operate.
Crowning compensation
u Low worktable has an automatic crowning compensation uint; compensation amount is automatically set up by CNC system,with guarantee a same bending angel on full length.
u The worktable adopts the particular design,reducing the crowning distortion amount of lower tool effectively.
CNC control system
u CNC control is DA52,DELEM of the Netherlands
Dies and tool configuration
List of main commercial components:
Serial | Name | Supplier |
1 | CNC system | |
2 | Servo motor | |
3 | Servo drive | |
4 | Hydraulic system | |
5 | High pressure gear pump,proportional direction-flow valve,pressure-control valve,change valve,one-way valve,pre-fill valve,shuttle valve,retainer,pressure equalizer,damp bolt,high pressure oil filter | Rexroth/ Hoerbiger,Germany |
6 | Optical readout | Haidenhain,Germany |
7 | Slide-in joint of hose | EMB,Germany |
8 | Ball screw,linear guide | HIWIN |
9 | Seals of cylinder | VALQUA,Janpan |
10 | Main motor | ABB |
11 | AC contactor/Heat relay | Schneider,France/Siemens,Germany |
12 | Single/double pole air switch,button |
Control Technology
The synchronization of
press brake adopt the technology of full loop electro hydraulic
servo control, the positioning signal of the upper beam are feed back by raster (light-ruler) to CNC system and CNC system will check the opening size of synchronization valves, adjusting the inlet oil amount, to realize the synchronizing movements of the upper beam (Y1, Y2), and keep the worktable are always parallel situation. Following the situation of sheet metal to be bended, CNC system control automatically the amount of the crowning compensation of worktable to realize that angle being bended of workpiece can keep same along the full workpiece length.
Crowning Compensation
Crowning compensation system on worktable can make a workpiece having a same precision full along the length of the workpiece. A crowning compensation system is composed of a group cylinders in line in worktable, which can from a relative movements of worktable, forming a curve needed of adding conves to worktable, to ensure unchanged the relative position to the upper beam of worktable after the worktable being under pressure. The crowning compensation amount is automatically calculated out by CNC system according to the worktable's situation.
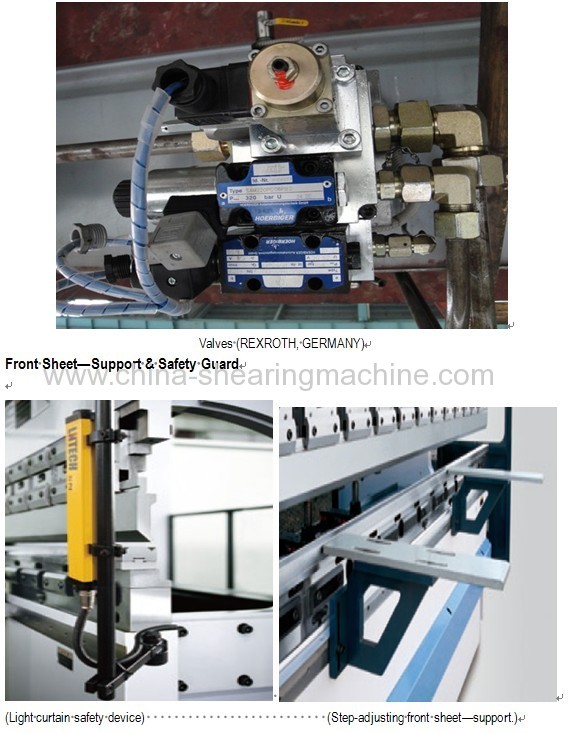