Typical characteristics
- Processing the powder from the fluidized powder hopper
- Quick and simple color change
- Supplied ready for use
- Available with one or two guns (extensible)
CL-131S Electrostatic Powder Manual Coating Equipment,is designed exclusively for electrostatic coating with powder.
CL-131S Series Features and Specifications:
0-100 Digital Adjustable KV
Fully Adjustable Amperage
Interchangeable with the Gema original equipment OPTIFLEX
Fully Adjustable Air for Pump on Pressure, Dosage and Nozzle Rinsing Air.
Comes with Full Array of Nozzle Assortment.
Field Tested and Proven to operate in the toughest environments.
Comes with different array of delivery systems:
Because this system is specially balanced for the maximum spray capability with
the Smoothest Finish Possible.
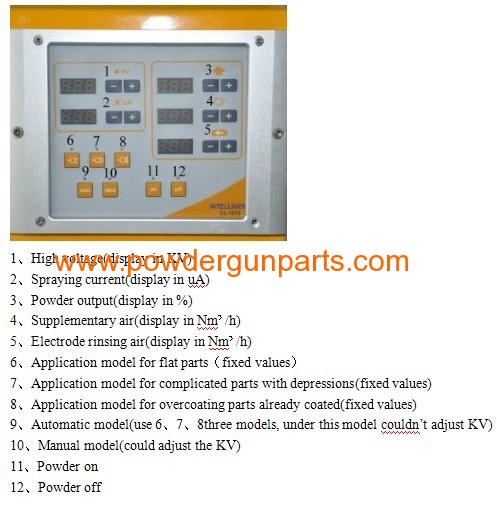
Configuration:
A control unit power supply cable
- A air filter
- A air pressure regulator
- A fluidized powder hopper
- A plug-in injector
- An manual powder gun with gun cable, powder
hose, rinsing air hose and standard nozzle set.
- Pneumatic hoses for conveying air (red), supplementary
air (black) and fluidizing air (black)
powder hose
Ground wire
TECHNICAL DATA
Electrical data | | |
Mains input voltage | 100-240 VAC | |
Operating frequency | 50-60 Hz | |
Input power | 50W | |
Nominal output voltage (to the gun) | max. 12 V | |
Nominal output current (to the gun) | max. 1 A | |
| IP54 | |
Ambient temperature range | 0°C - +40°C (+32°F - +104°F) | |
Max. operating temperature | 85°C (+185°F) | |
Approvals | CE | |
| | |
Pneumatical data | | |
Compressed air connection | 1/4" male quick release | |
Max. input pressure | 10 bar / 145 psi | |
Min. input pressure (while unit in operation) | 6 bar / 87 psi | |
Max. water vapor content of the compressed | air 1.3 g/m³ | |
Max. oil vapor content of the compressed air | 0.1 mg/m³ | |
| | |
Packing Dimensions | | |
Length | 120CM | |
Width | 79CM | |
Height | 73CM | |
Weight | approx. 55kgs | |
| | |
Connection Description | | |
1.1 Air In | Compressed air connection (6-10 bar / 87-145 PSI) | |
2.1 Power | Mains cable connection (100-240 VAC) | |
2.2 Gun | Gun cable connection | |
1.4 | Electrode rinsing air connection |
| |
1.3 | Pict | |
1.2 | | |
Grounding connection | Pict | |
Packing Dimensions
Length:69cm
Width:52cm
Height:56cm
Weight:37 kgs.
the powder gun through the powder hose . The powder is electrostatically
charged at the nozzle of the gun. In addition, an electrostatic field is
created between the gun nozzle and the grounded object. The charged
powder spray remains adhered to the surface of the object.
The powder is fluidized by air forced through a porous plastic plate from
below. The powder acquires, thereby, fluid-like characteristics.
The conveying air, supplementary air, and rinsing air are set on the control
Unit
Theprocess of the coating is like this: The powder is fluidized in thepowder hopper. The injectors transport the powder through the hoses tothe guns. The guns spray a powder/air mixture onto the workpieces
related equipments
spray booth
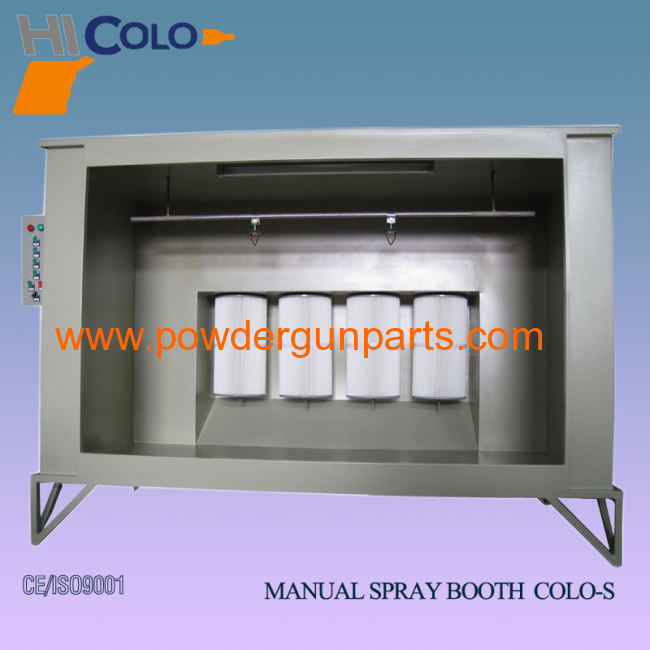
This popular size for small shops measures 1700mm inheight by2400mm in width by1 500mm in depth . Our Powder Booths makeefficient useof shop space and are designed for manual "batch" orautomated/processpowder coating with or without overspray reclamation.Shop air is drawninto the powder coating spray booth, and then passesthrough the powderbooth's workspace into a filtered plenum integratedinto the wall(s). Theair is filtered in multiple stages and thendischarged to the outsideatmosphere or routed back into the room.Disposable filters are easy toinspect and replace.
. FUNCTIONS
1.manual booths are the right solution for every application: fornewstart up and experienced users alike, or as a one-off solution forsmallor medium series.
2. A space-saving design,integrated functions and ease ofoperationprovide ideal conditions for efficient and high quality manualcoating.
3.by maintaining the airflow at design levels. During operationoverspraypowder accumulates on the cartridge filters. As the cartridgefiltersload, airflow decreases and negative pressure rises within theairhandler. A timer activates a system of air purging valves that clearthecartridge filters of accumulated powder to ensure maximum life.
The powder coating process
The powder coating process involves three basic steps:
- Part preparation or the pre-treatment
- The powder application
- Curing
Part preparation processes and equipment
Removalof oil, soil, lubrication greases, metal oxides, welding scalesetc. isessential prior to the powder coating process. It can be done byavariety of chemical and mechanical methods. The selection of themethoddepends on the size and the material of the part to be powdercoated,the type of soil to be removed and the performance requirement ofthefinished product.
Chemicalpre-treatments involve the use of phosphates or chromatesin submersionor spray application. These often occur in multiple stagesand consistof degreasing, etching, de-smutting, various rinses and thefinal phosphating or chromatingof the substrate. The pre-treatmentprocess both cleans and improvesbonding of the powder to the metal.Recent additional processes havebeen developed that avoid the use ofchromates, as these can be toxic tothe environment. Titanium zirconiumand silanes offer similar performance against corrosion and adhesion ofthe powder.
Another method of preparing the surface prior to coating is knownas abrasive blasting or sandblastingand shot blasting. Blast media andblasting abrasives are used toprovide surface texturing and preparation,etching, finishing, anddegreasing for products made of wood, plastic,or glass. The mostimportant properties to consider are chemicalcomposition and density;particle shape and size; and impact resistance.
Siliconcarbide grit blast medium is brittle, sharp, and suitablefor grindingmetals and low-tensile strength, non-metallic materials.Plastic mediablast equipment uses plastic abrasives that are sensitiveto substratessuch as aluminum, but still suitable for de-coating andsurfacefinishing. Sand blast medium uses high-purity crystals thathavelow-metal content. Glass bead blast medium contains glass beadsofvarious sizes.
Cast steelshot or steel grit is used to clean and prepare thesurface beforecoating. Shot blasting recycles the media and isenvironmentallyfriendly. This method of preparation is highly efficienton steel partssuch as I-beams, angles, pipes, tubes and large fabricatedpieces.
Differentpowder coating applications can require alternativemethods ofpreparation such as abrasive blasting prior to coating. Theonlineconsumer market typically offers media blasting services coupledwiththeir coating services at additional costs.
Curing oven
manufacturer curing conveyor oven used for curing the workpiecewhichhas been spraying during the powder coating. When a thermosetpowder isexposed to elevated temperature, it begins to melt, flows out,and thenchemically reacts to form a higher molecular weight polymer in anetwork-like structure.
Powder coating oven have a galvanized steel sheet on outside and steel sheet on the inside.
- Structure:consist of Body,insulation, cover, heater(stainlesssteel heater withHeat Sink).use electricity to create the energy,through the circulating fan ,make the temperature in the oven to riseuniformly. Then make the temperature of workpiece to rise.
along with a built-in track to roll your powder coating racks into the ovens.
Model | COLO-O-1 |
Overall dimensions | 1500 width x 1700 height x 3000 depth |
Power supply | GAS |
Voltage | 110V/220V |
Frequency | 50-60Hz |
Door type | Double sided, drive-through |
Warm-up time | 15 min. (180-220° C) |
Homogeneity | < ± 3°C if 185°C |
Temperature stability | < ± 1°C |
Temperature max. | 230° C |
Transport | Top |
Air circulation | Forced |
Band of burner | Italian Riello |
Capacity | 7650L |
Warranty | 12 months |
A, make sure the ground is level.
B, clean the inner of the oven, close the door.
C,make the workpieces which will to be cure ready. About half an hour.
D, Set the temperature as you required, normally for180°C-200°C.set the time you need to cure, such as 25 minutes (this willaccordingto thickness of your workpiece, if for thin,then 20mins,forthicknessabout 25mins).open the door, push the workpieces into theoven,close thedoor.
E, turn on the power switch,and then press the bottom of turn on
F,After the temperature reach to the value we setted, the time willbeginto change.(you don't need to operate, it is automatic change )
G, When hear the bell ring, press the bottom of turn off ,push out the workpiece which has been cured. Push into the next batch.
H, please lift down the the workpiece which from the oven after cured ,after it will be cooled.
We provide stock or custom-built powder coating ovens.
All oven dimensions are interior
There is a one-year warranty on all electrical componets
Please allow us 2-3 weeks to build after you placing order.