4-station High Speed and Fully Automatic Cold Heading Machine, Multi-station Cold Heading and Forming Machine
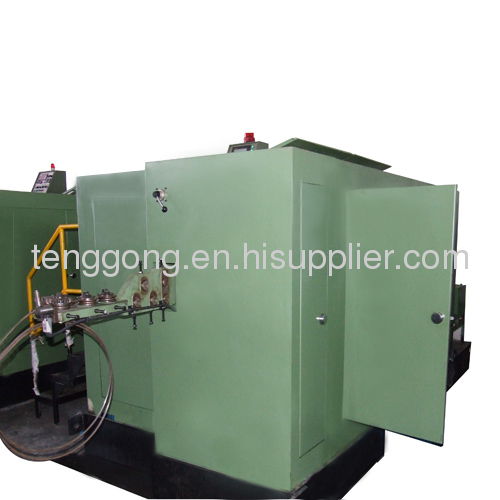
Product performance of
Multi-station Cold Heading and Forming Machine, 4-station High Speed and Fully Automatic Cold Heading Machine:
1.The main body of
Multi-station Cold forge Forming machine is made by high quality host casts and through second tempering treatment to ensure that whole machine can keep good and last longer.
All the moving parts are made by the best material and through best special technical treatment which can improve capability and ensure the machine life.
2.The key parts are made by numerical control machine and CNC to ensure the precision which can make the machine more stable and lower the noises.
3.We use famous hydraulic components and pneumatic components to ensure the stability of machine and the force lubrication system make every moving parts always running under a good lubrication environment.It is a good way to longer a machine's work life.
4.The major motor controlled by frequency converters and the driven system adopted pneumatic clutch device and pneumatic brake device to ensure the sensitivity and make the adjustment more easily and more quickly.
5.The electric control system adopted PLCS which can ensure the whole machine always in a normal way and auto deal with different kinds of failure.
6.The whole machine adopted seal completely design which can improve the safety and make the environment more cleanly.
Main Features of Multi-station Cold Heading and Forming Machine, 4-station High Speed and Fully Automatic Cold Heading Machine:
1.Manipulator with rotary swing clip feed means and pneumatic clamping force, is not only stable but also can adjust the pressure according to different products avoid crushing the products.
2.The rear knock out mechanism can be individually adjusted with front dead point in the same position.
3. Feeding system of ratchet pawl wheel is stable, reliable and convenient to adjust.
4. Cross movement of the machine driven by double-cam above the shaft makes it easy to adjust the operating compatibility of the machine.
5. The cams in various positions are calculated and designed by the computer, and then machined and manufactured by CNC machine tool to ensure smooth and precise curves.
6. Side plates apply imported quenched high-carbon alloy steel SKS to maintain stable precision of main sliding table in long term.
7. A PLC controlled safety checking system can automatically detect the performance of key system and display of any abnormality.
8. Imported inverter is equipped for easy adjustment of stepless output speed.
9. As an optional, CNC system of "man-machine interface" can be equipped to automatically adjust the dimension of rear knock-out threaded pipe, stop position and feeding length, greatly saves mould renewal and adjusting time. With a memory capacity of 99 digital modules, it is suitable for fast change over of moulds.
Specifications | Unit | TGBF-134LL |
Forging station
| No. | 4 |
Forging force
| Kgs | 130,000 |
Max cut-off dia.
| mm | φ15 |
Max cut-off length
| mm | 285 |
Speed Range
| pcs/min | 50-80 |
P.K.O Stroke
| mm | 30 |
K.O Stroke
| mm | 280 |
Main Slide Stroke
| mm | 380 |
Main motor power
| kw | 37 |
Cut-off-die size
| mm | φ55*70L |
Punch die size
| mm | φ60*229L |
Main die size
| mm | φ86*305L |
Die pitch
| mm | 110 |
Machine Weight(Approx)
| kgs | 38,000 |
Normal bolt size
| mm | 8-12.7 |
Shank length of blank
| mm | 75-260 |
Models apply air clutch brake with small starting current, allowing operation modes of "Inching", "Single Stroke" and "Continuous Running". The main sliding table can automatically stop at its rear position while operated under "Single Stroke" and "Continuous Running" modes, so as to obtain maximum space for adjustment.