DM-QMC is currently the most complete answer to the growing requirements of concepts like JIT (Just In Time) and SMED (Single Minute Die Exchange) in all advanced manufacturing process to face smaller production batches and wider product ranges, by offering.
DM-QMC is using electrical impulses to open and close magnetic mould replacement system. Using the different characteristics of different magnetic materials designed to best magnetic circuit, Through the electronic control system for the distribution of internal magnetic circuit control and conversion, Make permanent magnet field in the system itself balance, The external characterizationThe external characterizationThe external characterization is demagnetization or relaxation state; Or released into templates work surfaces, The external characterization is magnetization or mould clamping state.
1850T Injection electro-permanent magnetic quick mould change Systems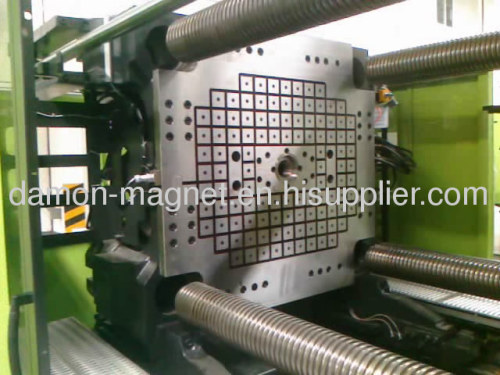
During the
Mag phase the magnetic flux is short-circuited outside the magnetic surface safely clamping the mold with a very limited magnetic depth so as not to affect any internal part of the engaged mold.
During the
Demag phase the magnetic flux is short circuited inside the magnetic module frame,perfectly releasing the mold for its changeover.
A magnetic clamping mould avoids deformation and avoid the effect of internal tension.Clamping force evenly distributed throughout the contact surface, Rather than a traditional clamping press several points, Make mould injection molding, stamping out products maintain consistency.
Proximity sensors:
An inductive proximity sensor located in the "neutral" area detects the presence of the mold to enable the
activation of the magnetization cycle.The 0,2 mm (0.0078 in) threshold value prevents any "open field magnetization" to grant the operator safety and it immediately halts the machine functions in case of mold detachment. The full safety for the operator is also granted.